College of Engineering’s Virtual Design Showcase
The Engineering Design Showcase is the culminating experience for graduating seniors. This event brings together project teams from all eight departments for an opportunity to share their design projects with their peers, professors and the public. This year, the College of Engineering will host the showcase virtually on the UC Davis Now app. Although this event has shifted online, more than 120 senior design teams and engineering clubs have signed up to share their efforts with industry partners, alumni and the campus community.
These evaluators will provide feedback on elements such as the team’s ability to identify, formulate and solve an engineering problem, as well as the team’s skills in communication, teamwork and adherence to current engineering standards and techniques. They will have an opportunity to review the abstracts, posters and any additional media to make evaluations. This feedback is central to the showcase and the college thanks the companies, corporations and individuals who have generously supported and volunteered their time for this event.
If you are an evaluator or are interested in checking out all of the design projects, click here. This link will be live and accessible on Thursday, June 4.
A look at some of this year’s project teams:
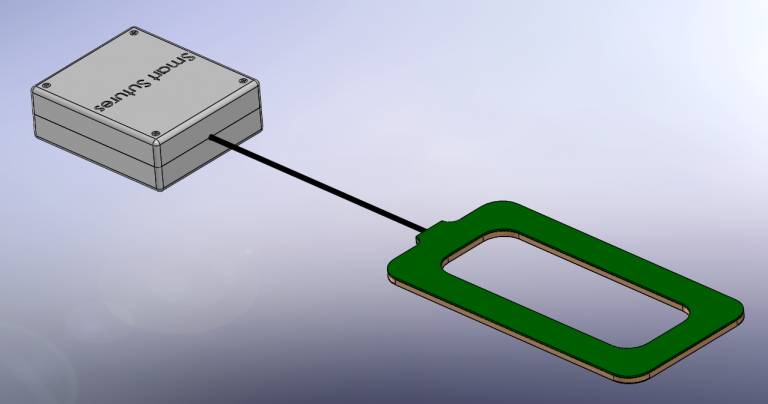
Smart Suture: A Wound Monitoring Dressing
A team of biomedical engineering students designed Smart Suture, a post-surgical device containing multiple sensors to detect surgical site infections (SSIs) as early as possible after surgery. Currently, there are methods of combating SSIs after they form, but there are few reliable methods for early detection and the responsibility falls on the patient to watch for infection-like symptoms. The team has created a device that detects when temperature or swelling at the surgical site increases above unacceptable levels and warns the patient and clinician.
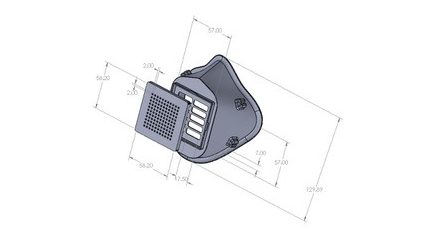
3D-Printed Biodegradable Mask Created with Extruded PHA Polyester
The COVID-19 pandemic has prompted a massive at-scale production and use of protective face masks made from polypropylene and other plastics. The throwaway culture that has developed around disposable masks only perpetuates the existing issue surrounding rapidly accumulating plastic waste. Driven by an urgent need for reusable biodegradable masks, a team of biological and agricultural engineering students designed a protective face mask that includes an outer shell that will fit a variety of different faces. This mask also contains a filter specifically designed to be FDA approved to avoid the spread of germs that cause viruses such as COVID-19. The mask is created with a 3-D printer using PHA filament, a biodegradable polyester.
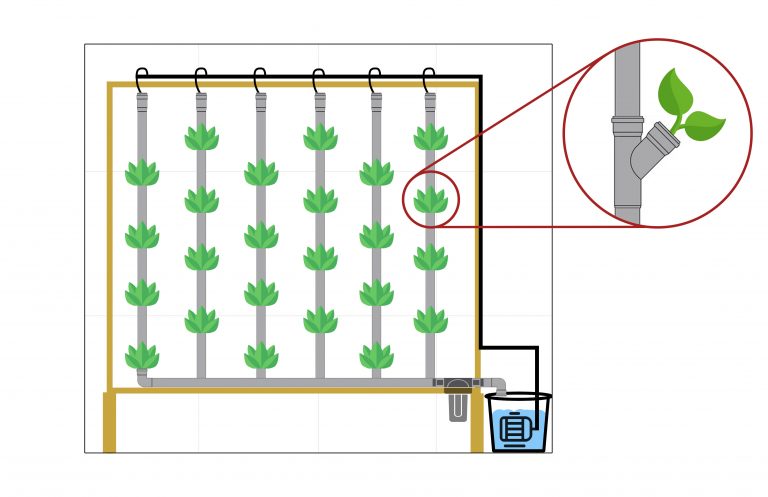
Smart Greenhouse to Inspire Future Generations to Grow Sustainably
A team of biological and engineering students developed a smart greenhouse that will be used to educate students on sustainable indoor farming. The team’s greenhouse design features an aeroponic growth system that efficiently grows plants by using less water than conventional farming. To power the greenhouse, the team implemented a photovoltaic system that is functional off-grid. The greenhouse maintains an automatic control system used for plant growth. This is performed with microcontrollers, sensors and actuators to engineer a controlled environment. Once physically executed, the greenhouse will serve as a place for students to develop new sustainable methods for vertical farming technology through the years. Learn more here.
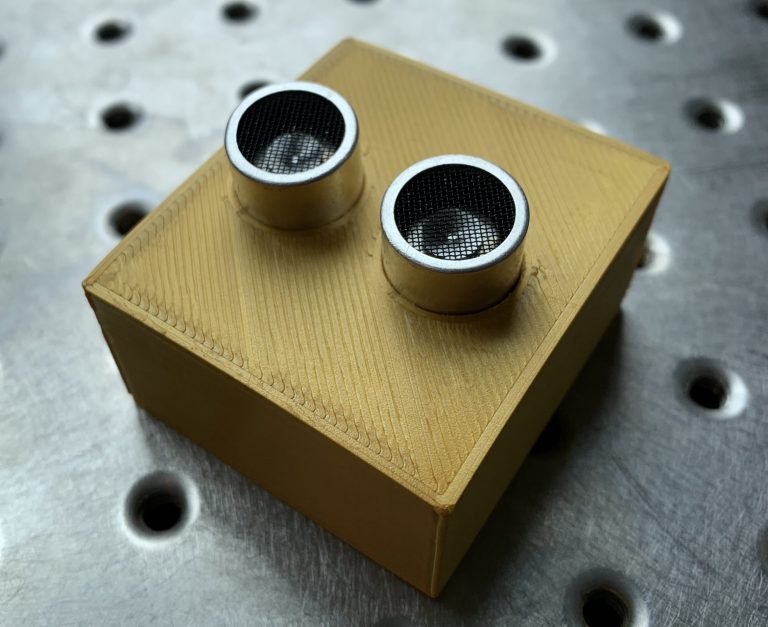
Relod: Smart Storage for Smarter Purchases
Relod is a device that can turn any normal container into a smart container. By implementing a series of sensors and Amazon API (application programming interface), a team of electrical and computer engineering students created a device that will inform users of the current content level of their containers as well as place orders to replenish the supplies after certain thresholds are passed. The team’s goal is to eliminate the waste of ordering too much too soon and the inconvenience of ordering too late. By using their device, users will be able to save time and money by having a fully customizable system to keep track of their recurring purchases.
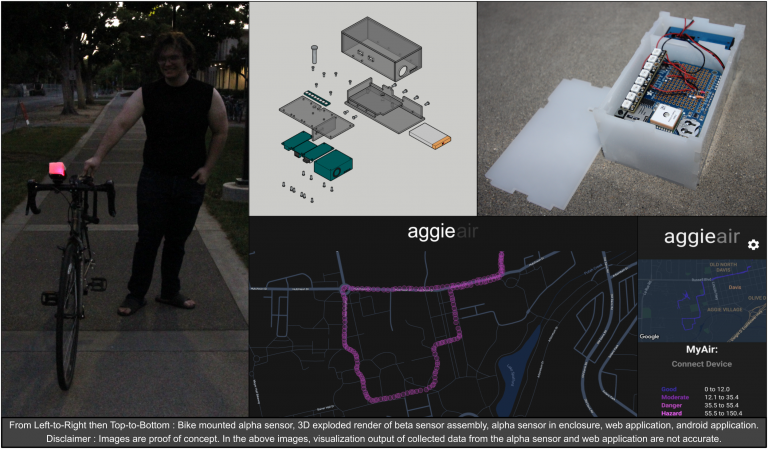
AggieAir
Under the guidance of Emily Schlickman, assistant professor in the UC Davis Department of Human Ecology, a team of computer science students developed a pilot project called AggieAir to create a series of low-cost, bike-mounted and DIY (do it yourself) monitoring devices to collect community-level data on localized air quality. This device generates 2.5 μm particulate matter data instantaneously in the form of a color-changing bike light, as well as gathers these data for upload to a collaborative data set. Examples of particulates in this size range include fine dust and dirt, as well as combustion particulates that can stem from vehicle emissions and wildfires. The team’s web-based application visualizes this large data set in the form of geospatial maps. This is the first step in creating a documented platform with the goal of empowering the public to build their own device and raise awareness on particulate matter pollution.
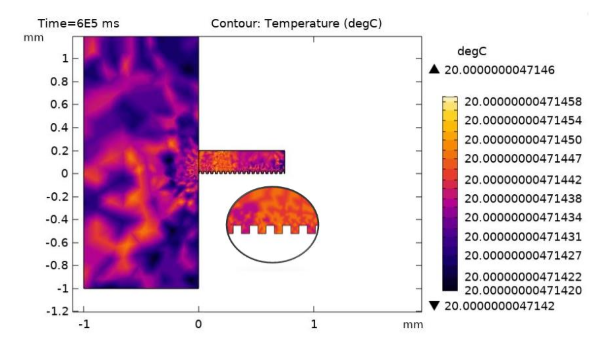
Design and Modeling of Thermal Dissipation System for Augmented Reality Glasses
These materials science and engineering students are working closely with OSRAM Opto Semiconductors to design and model a system for optimal thermal dissipation for their augmented reality (AR) glasses. OSRAM’s AR glasses contain two sets of RGB lasers that are utilized for near-to-eye projection, eye tracking and proximity sensing. The red laser fails when the junction temperature, found between the red laser and the aluminum nitride wafer it is attached to, reaches 70°C. The team’s goal is to increase heat dissipation to reduce the junction temperature to 65°C. Design recommendations will be made to reduce the junction temperature in hopes of experimental replication and implementation into OSRAM’s AR glasses.
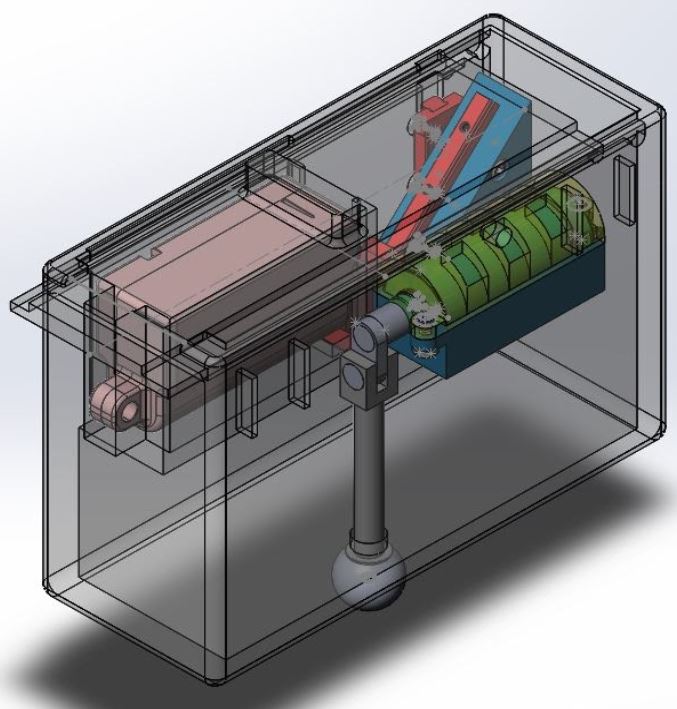
Movement Feedback System for Robotic Hand
A team of mechanical and aerospace engineering students designed a vibrating mechanical system to serve as part of a robotic prosthetic hand to be used by amputees. This system is made of a pushing head that extends and vibrates against a user’s arm muscles to create the illusion of movement in the missing hand. If the pushing head vibrates at a certain frequency, the amputee can “sense” that their hand is moving. Because the system will be attached to the user’s arm, it must be small enough to prevent any interference with the regular use of the prosthetic, ensuring no obstructions or difficulties in movement or usage occur. This system will have the ability to move along with the user at a speed that allows for the constant illusion of motion, such as with the flexing or extending of the user’s bicep. A DC motor with a physical attachment will spin and produce a lateral force into the user’s muscle to produce the required frequency. A linear actuator will be installed to help move the DC motor vertically in accordance to arm and muscle movement. A strain gauge is placed to read the strain created by the movement of the user’s muscles. This project is motivated by amputees’ needs to feel better connected to their prosthetic, which will cause lower abandonment rates of electronic prostheses.