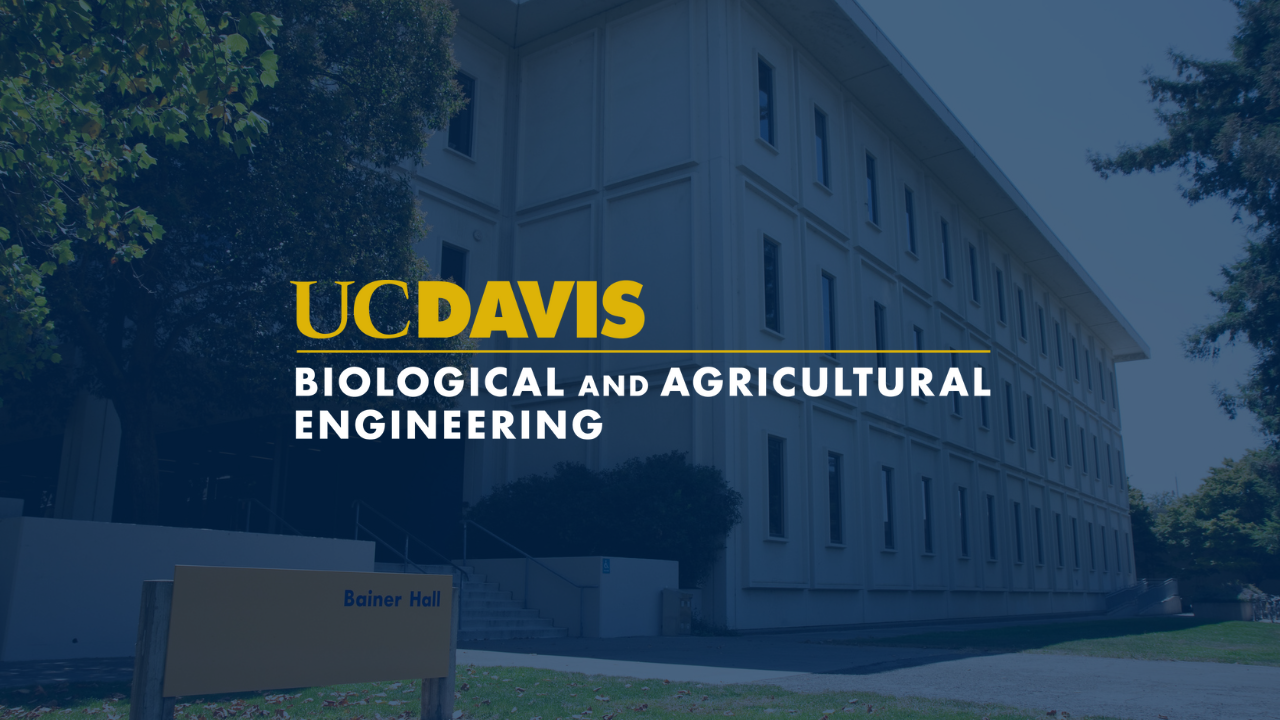
Event Date
Despite recent significant developments in Additive Manufacturing (AM) technologies, from printing materials to processes, light and heat are still the only energy sources used in AM to drive chemical reactions or physical transformations. Therefore, materials in AM processes are limited to photo sensitive resins, like in Sterolitography (SLA) or Direct Laser Writing (DLW), and thermoplastic filaments or powders, like in Fused Deposition Modeling (FDM) or Selective Laser Sintering (SLS). Parameters controlling the chemical interactions are defined by the amount of energy per molecule, interaction time and pressure which are the control parameters in the islands of chemistry. Conventional AM energy sources, light and heat, do not utilize the maximum potential of the chemistry in terms of the control parameters. Sonochemistry pushes these parameters to their limits. Extraordinary high temperature (exceeding 15000 K), high pressure (exceeding 1000 bar) and fast heating and cooling rates (over 1012 K/s) inside the active cavitation bubbles induced by sound waves surrounded by liquid at ambient-temperature, are the reasons for the sonochmeical reactions. Direct Sound Printing is an invention that unleashes the potential of sonochemistry in AM processes, an unconventional route for printing impossible to print materials with conventional energy sources. In addition, sound waves can penetrate deep through physical objects that is out of reach for light and heat sources in common AM technologies. This concept lays the groundwork for printing at remote and inaccessible locations and introduces unique applications for remote maintenance in aerospace industries or in medical fields for remote printing of implants inside body.