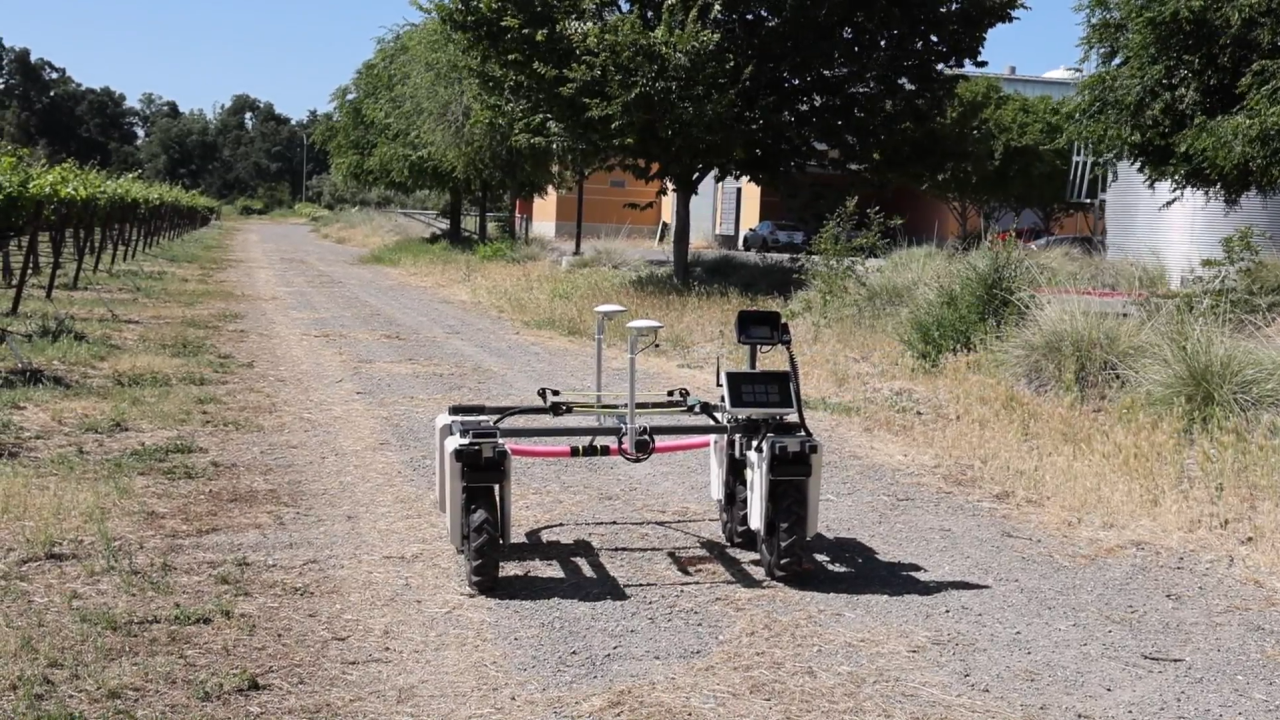
UC Davis Students Win Big at Inaugural Farm Robotics Challenge
The national competition asks students to create automated solutions to production issues on the farm
Quick Summary
- Engineering students and postdocs won the competition's grand prize of $10,000 for a robot that may increase worker safety and assists with harvesting.
- An interdisciplinary team of undergraduates won the Elegance in Design prize with a targeted spraying robot built from commonplace objects like PVC pipes and tie-down straps.
Two robotics teams from the College of Engineering at the University of California, Davis, developed winning designs for the inaugural Farm Robotics Challenge, a national competition for college students to create automated solutions to farm production challenges.
Out of 19 participating groups, the Amiggie team took home the event's grand prize of $10,000 for a robot that can monitor the posture of farmworkers for injury reduction and assist with harvesting crops.
Team Robo-ag, with students from the Colleges of Engineering and Letters and Science, received $5,000 and the Elegance in Design Prize for its assistant that can spray liquids, such as fertilizer or pesticide, on specific plants in a farm using GPS pinpoints.
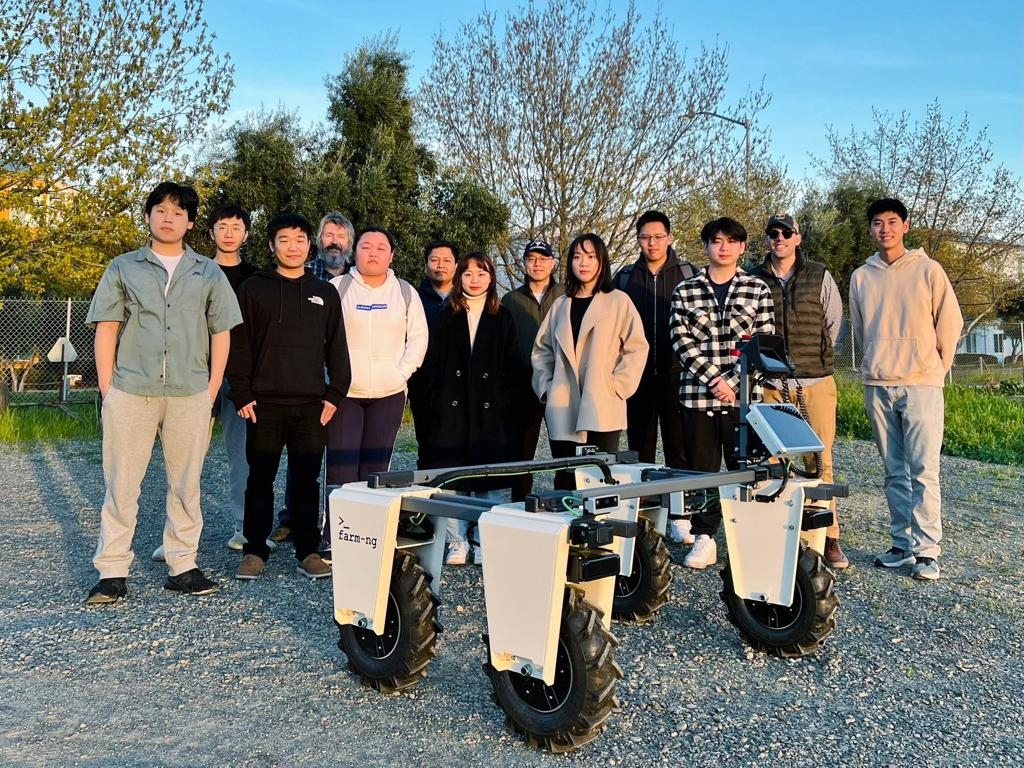
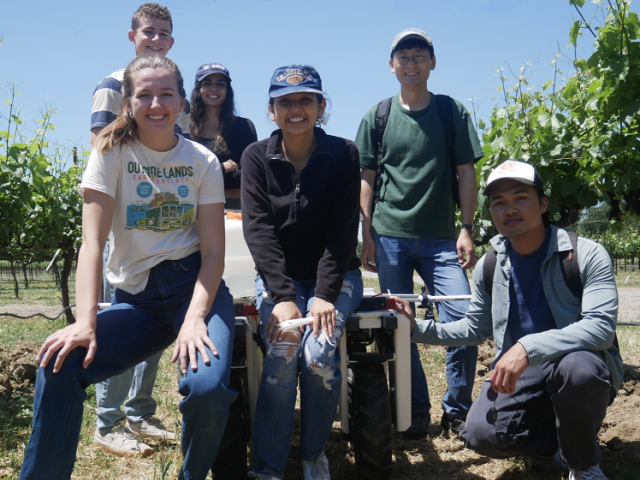
Each team started out with the same piece of equipment, a robotic tractor known as the Amiga. The sophisticated technology uses an Nvidia computer powerful enough for machine learning, two artificial intelligence-enabled cameras, and an all-electric tractor design capable of carrying 900 pounds.
The teams had to augment the platform with new hardware, software or both to perform and automate an essential farm task, such as weeding. While the robot could address all crop or farm size issues, the competition prioritized designs that were optimized for small farms due to their potential for greater impact.
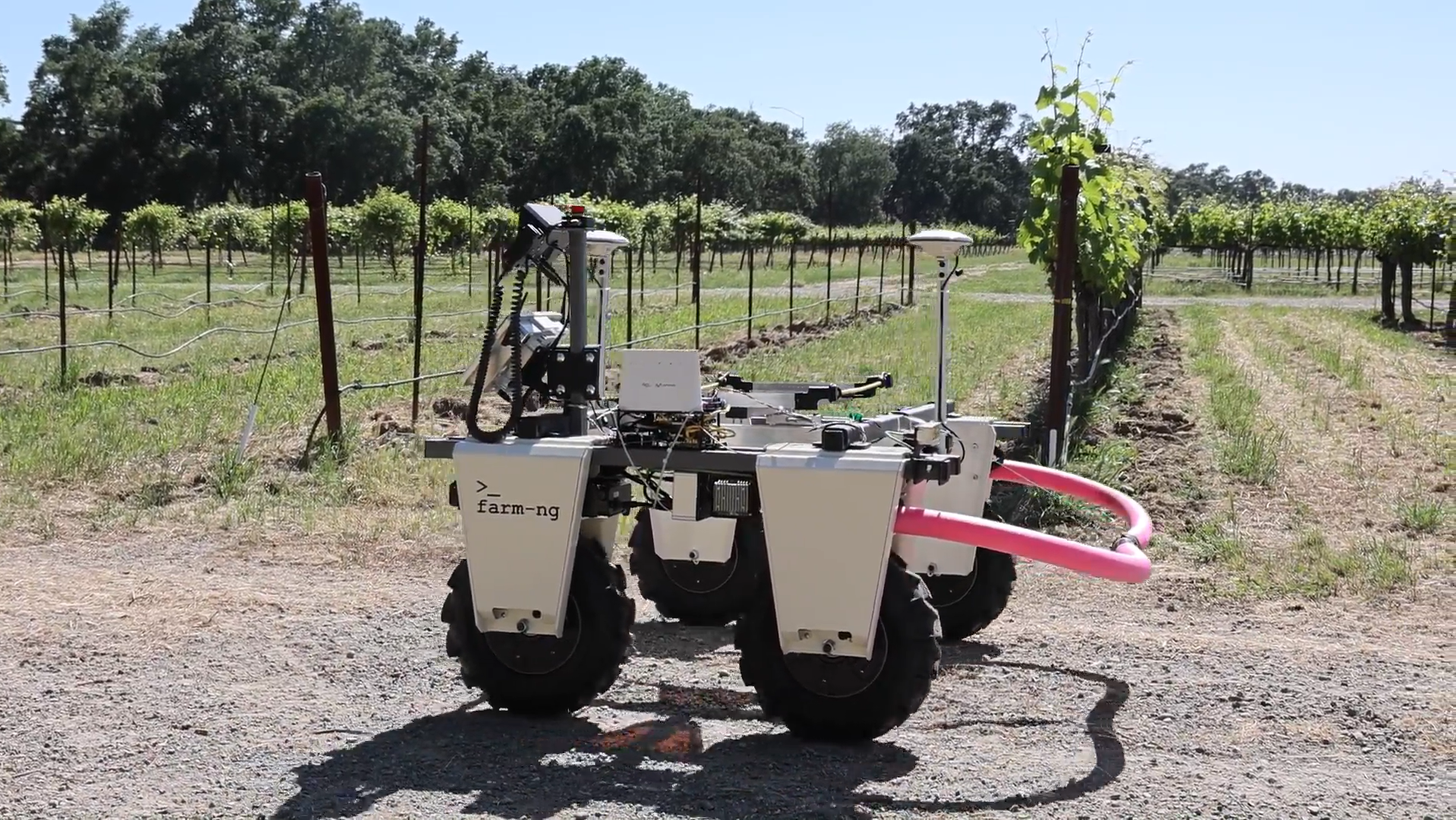
Every design was judged based on how well it met criteria ranging from its commercial and market potential to its overall cost.
The developers of Amiga — Watsonville-based agricultural robotics startup farm-ng — organized the annual event with the AI Institute for Next Generation Food Systems, The VINE and Fresno-Merced Future of Food.
"The Farm Robotics Challenge is about shaping the future of agriculture by inspiring the next generation of ag-tech pioneers," said Gabe Youtsey, an organizer for the competition and founder of The VINE.
"The ideas that emerged from this competition are solutions for today's farming challenges, highlighting how technology can contribute to a more sustainable, productive and resilient food system."
Safety First
The grand prize-winning Amiggie, a clever combination of Amiga and Aggie, started without safety in mind. The team intended it to be a harvesting assistant robot to detect when a payload of fruits or veggies reached its maximum weight and autonomously convey it back to an unloading point.
That was until one member made the team think deeper about the issue they were trying to solve.
"The idea behind a harvesting assistant robot is, at some point, to help reduce the workload of farmworkers," said Guilherme De Moura Araujo, a supervisor on the project and postdoc specializing in agriculture, health and safety in the Department of Biological and Agricultural Engineering, or BAE.
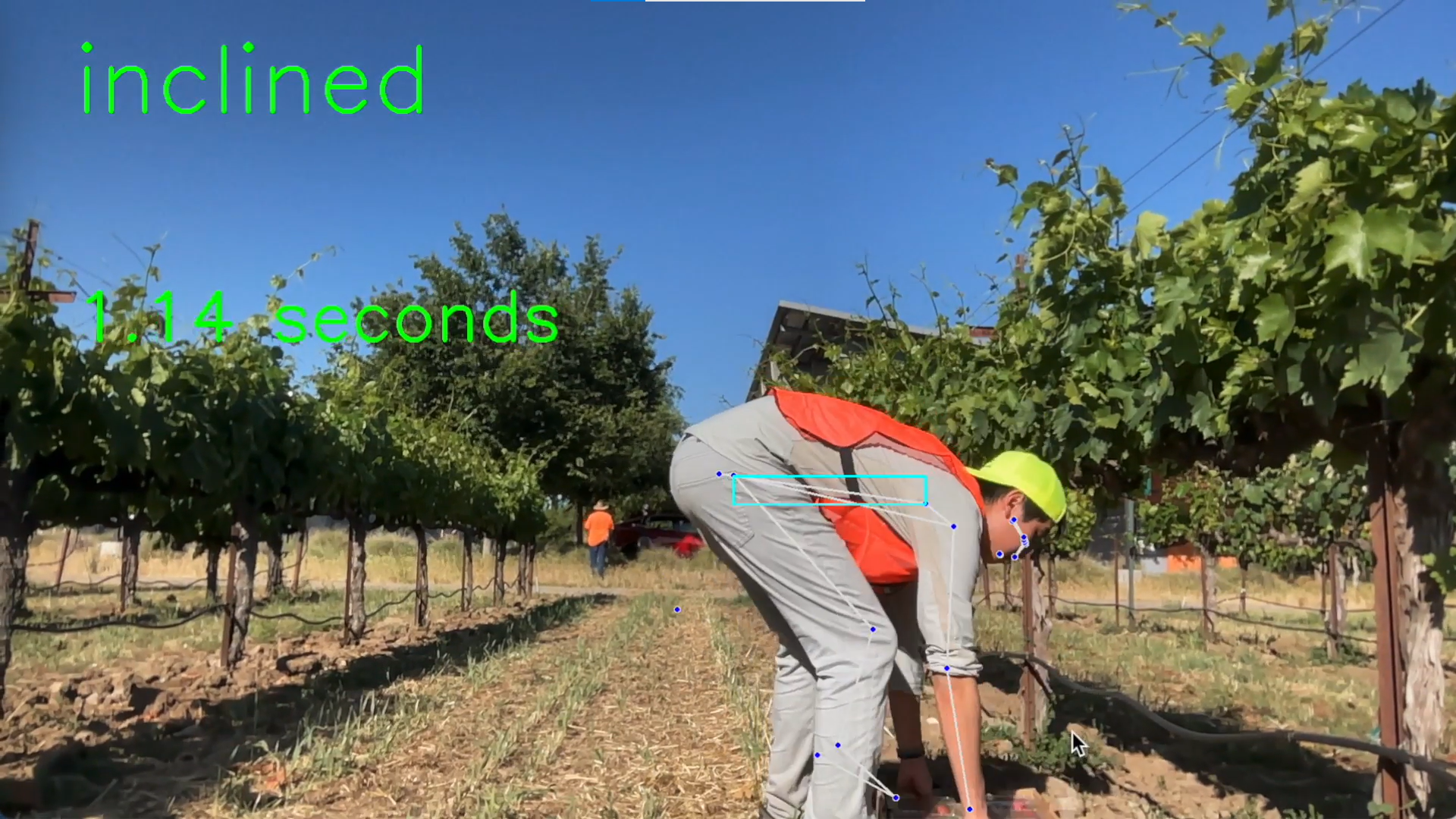
"Why not add more and also track [the farmworkers'] posture in real time to suggest micro-breaks for increased comfort and to decrease their exposure to occupational risks?"
He and his co-supervisor, fellow BAE postdoc Juan Fernando Villacres, inspired their team of electrical and computer engineering, mechanical and aerospace engineering and computer science and engineering students to adjust their design, adding a free machine-learning model developed by Google that uses video to track human posture. The team reworked the model so that it focuses on the hips, back and neck.
When the Amiggie notices that a farmworker has been in a position that may pose a risk for a period of time, such as being hunched over to pick strawberries for more than 15 seconds, it alerts the individual to make the necessary adjustments to their posture.
However, before the alarm goes off, the robot factors in things like how long the person has been working. Farmers can also easily set up the Amiggie to the needs of their farms, adjusting how long its alarm is set for certain positions.
"I think this is one of the things that the judges liked about our product," De Moura Araujo said. "We were not trying to reinvent anything or create anything from scratch. We were getting technologies that already exist and using them in a smart way with the capabilities of the robot to tackle a pressing problem."
Finding Depth in Simplicity
There's so much possibility in everyday objects, like the tie-down straps tucked away in the garage or the plastic container under the sink. The team behind Robo-ag saw these commonplace items as parts for a robot.
"Some of the other projects in the competition were like, 'Wow, that's really high tech,' while we're like, 'Okay, ours is some PVC pipes and tie-down straps, let's see what happens,'" said Summer Reeves '23, a biological systems engineer who helped build Robo-ag.
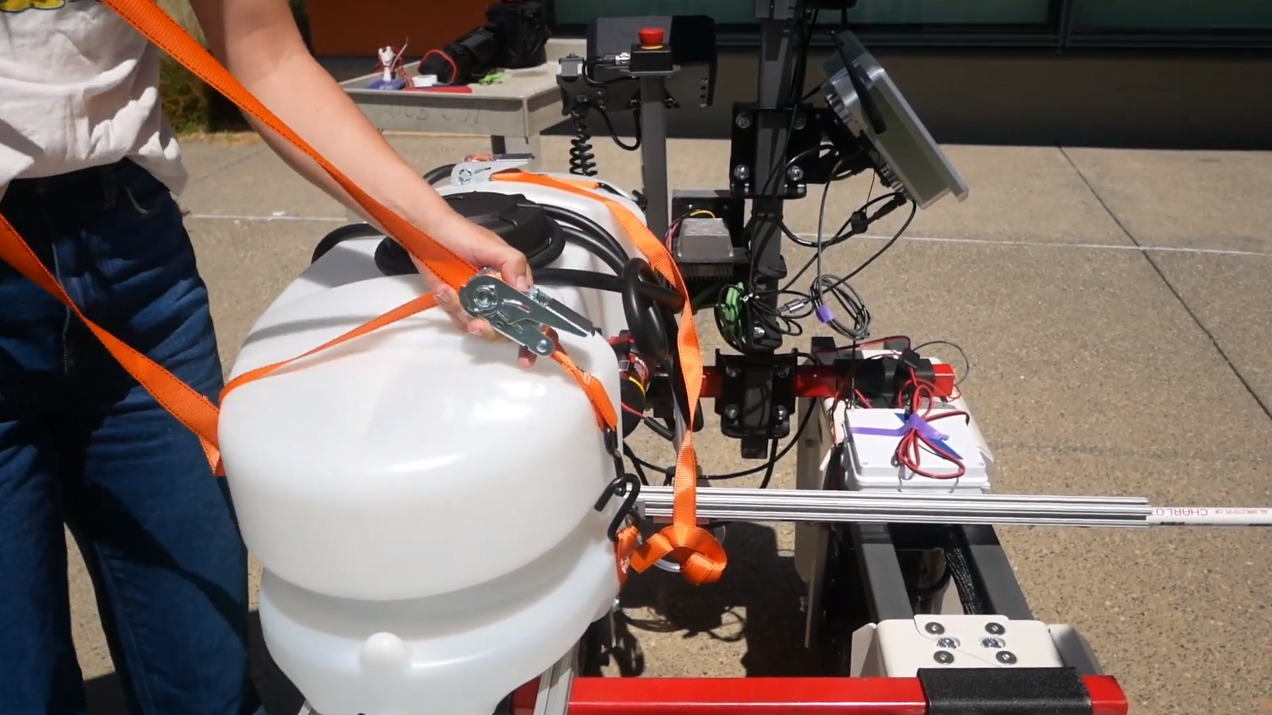
By keeping the technology simple with elements farmers likely have lying around their property, the team managed to make a complicated robot accessible, even to those that may have limited to no experience with robotics. It also kept building costs low and repair costs even lower.
"We tried to make [Robo-ag] as affordable as possible and were trying to use stuff that was already around [for its design]," Reeves said. "There's also a problem in the farm industry with farmers not being able to fix their own equipment. We wanted to make our hardware so if something broke, they could easily fix it."
Robo-ag minimally adds to the base Amiga platform, taking only a few minutes to set up with the largest item being a plastic tub affixed with tie-down straps. Connected to the tub are two targeting sprayers that are controlled by a piece of hardware that slides onto Amiga. The hardware allows the robot's computer to operate the sprayers, interfacing with the app that controls the whole device.
The appeal to keep things familiar extended to the application the team developed for Amiga's touchscreen computer, which the team named "Robo-ag" for simplicity's sake. With it, users can tell the robot which plants on their farm need fertilizer, pesticide or water by using GPS pinpoints, not unlike picking waypoints on Google Maps.
These pinpoints can also be modified to tell Robo-ag how much it needs to spray each plant. The green icon represents a one-second spray while the red is for three seconds, a precision that's matched by the sprayers themselves.
"The team started thinking about making the sprayers precise because there's a lot of runoff from fertilizers, pesticides and herbicides," said Vivian Vuong, a supervisor on the project and biological systems engineering doctoral student. "The targeted sprayers allow farmers to save money while also mitigating the environmental impacts associated with spraying on a farm."
While the team was not able to make Robo-ag fully autonomous by the time of competition, their aim is that one day it will allow small-scale farmers access to hands-free, precision spraying — technology that's typically very expensive to purchase and operate — at a very low cost.
Template for Success
The Amiga was both a formal constraint and a blank canvas for the competition, a fertile ground for the teams' innovative solutions.
It also offered an accessible entry point into robotics for UC Davis students, many of whom had no experience in the field.
"It was really eye-opening to see there are so many different applications of robotics," Reeves said. "I think there's a lot of ways to use it to advance the farming community and I'm definitely more open to that career path [than before]."
Hualong Yu '23, a computer engineering major and part of the Amiggie team, found the first-hand experience of the competition to be of great importance, especially as his senior design project.
"My team learned something new [and] made something of value for society," he said. "For us, for me, that is a big achievement. I also hope our success inspires more students to learn robotic technologies."