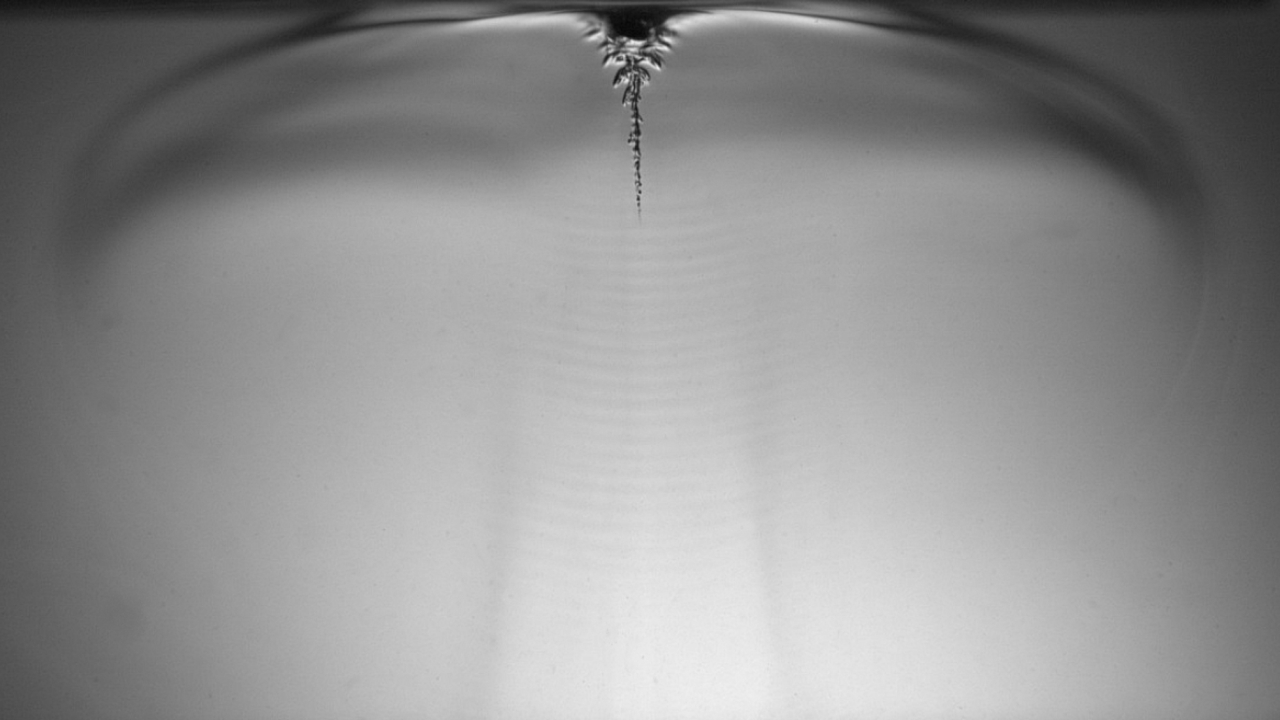
New Assistant Professor Aims to 3D Print Implants Inside the Human Body Using Sound
The silvery gray background of Mohsen Habibi's Zoom screen looks like a surreal and elegant image of an icicle slowly breaking the surface of a body of water and plunging into its depths.
What you are actually seeing is the first-ever footage of sound waves creating solid material out of a polymer solution from behind a physical barrier.

The novel 3D printing method depicted in this image, which won two scientific image awards, is called Direct Sound Printing, or DSP, and was developed by Habibi, a new assistant professor in the Department of Mechanical and Aerospace Engineering.
The technique is still in its early stages; Habibi and his colleagues at Concordia University in Montreal, Canada, first successfully printed an object with sound in the spring of 2018. So, while it requires fine-tuning and analysis, Habibi is optimistic about its potential applications.
"We could print implants inside the body without open surgery," he said, noting that the polymer material he has used to print is biocompatible. "Another application is the maintenance of regions that are not accessible. Let's say you're going to do a repair inside the fuselage [of an aircraft], somewhere that cannot be reached, that we would need to open or destroy it to do the printing or repair."
Using DSP in these scenarios would enable surgeons and engineers to work without opening anything because the soundwaves can penetrate through physical barriers to print on the other side, which is what Habibi was looking for when he started pursuing this research in 2017.
From Tiny Bubbles to a Major Discovery
Habibi wanted to see if he could do the 3D printing process without light, which is the most dominant method of 3D printing. Its main limitation, however, is its inability to penetrate opaque materials like metals or skin. To create chemical reactivity on opposite sides of a solid barrier, Habibi turned to sonochemistry, which deals with the interaction between sound and matter.
Habibi began investigating cavitation bubbles, or bubbles that occur when sound creates air in liquid materials. Those bubbles, he discovered, can create chemical reactivity at high frequency using ultrasound waves and convert the liquid resin to a solid polymer base.
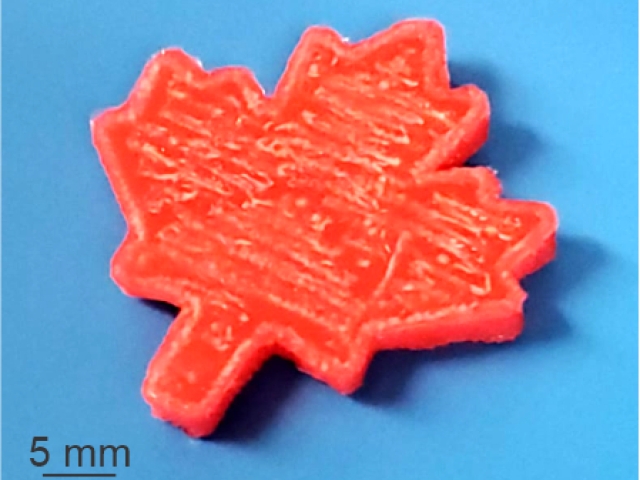
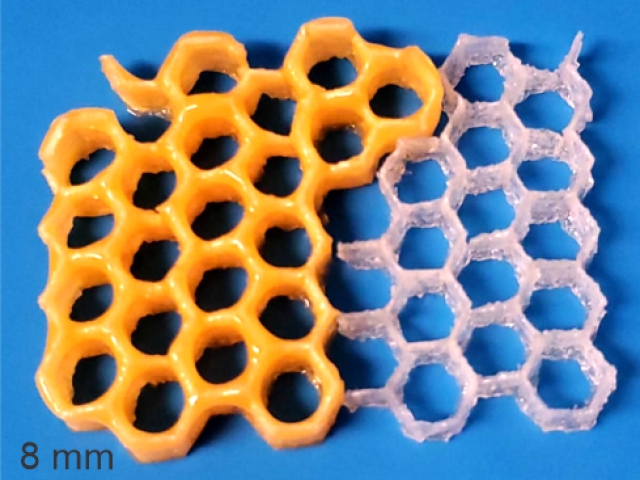
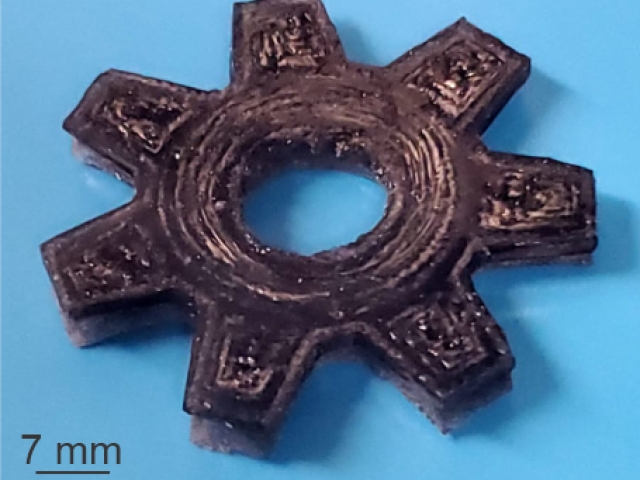
In his 2022 paper in Nature, printed polymeric objects have included shapes like a maple leaf, honeycomb, and gears, and Habibi has successfully printed ear and nose shapes using tissue phantom and real porcine skin, fat and muscle. Habibi and his colleagues are currently finalizing two new papers that explore the printing resolution and accuracy speed by redesigning the printing mechanism of his first work to print precise objects like microfluidic devices.
At UC Davis, he is eager to collaborate with the biomedical engineering department, veterinary medicine and UC Davis Health to research what is possible with this new technology, named one of the most significant scientific discoveries of 2022 by Québec Science, one of Canada's leading science magazines.
Building a Sound Foundation of Research
In addition to digging deeper into the applications of DSP, Habibi plans to investigate the fundamentals of the sound-printing process.
"We know what is happening overall, but we don't know what is really happening in those bubbles," he said. "We don't know exactly what temperature you're getting up to in there or the pressure that you're getting there. The fundamentals are not well-known, so it opens up a huge venue for basic research."
The foundation of Habibi's research is analysis and optimization of manufacturing using computer-aided design and manufacturing (CAD/CAM) processes. He has already built software platforms for General Motors and MAL Inc. to simulate machining processes and inspect components virtually.
Building on these processes, Habibi will create techniques that would allow manufacturing companies to analyze production issues using visual simulation and experimental data instead of having to inspect every single part within the mechanism.
Before joining UC Davis, Habibi was a research associate at Concordia University in Canada and a postdoctoral research fellow at the University of British Columbia. He earned his Bachelor of Science in mechanical engineering from the University of Mazandaran in Iran, as well as a master's degree in mechanical engineering from Amirkabir University of Technology and a Ph.D. in mechanical engineering from Concordia University.
In industry, Habibi was the senior manufacturing engineer for General Motors and a mechanical designer for space technology company MDA. He also cofounded Xwave3D Inc., which aims to "revolutionize additive manufacturing" using Habibi's patented DSP technology.
Habibi recalls how excited he and the other researchers in the lab were when he could print the first spot with the bubbles in the resin. They had created something new and real, and it took him back to why he was drawn to mechanical engineering in the first place.
"Making things got me into mechanical engineering. It's tangible because it's directly making things you can see. When we finally printed something, we knew we did something huge."