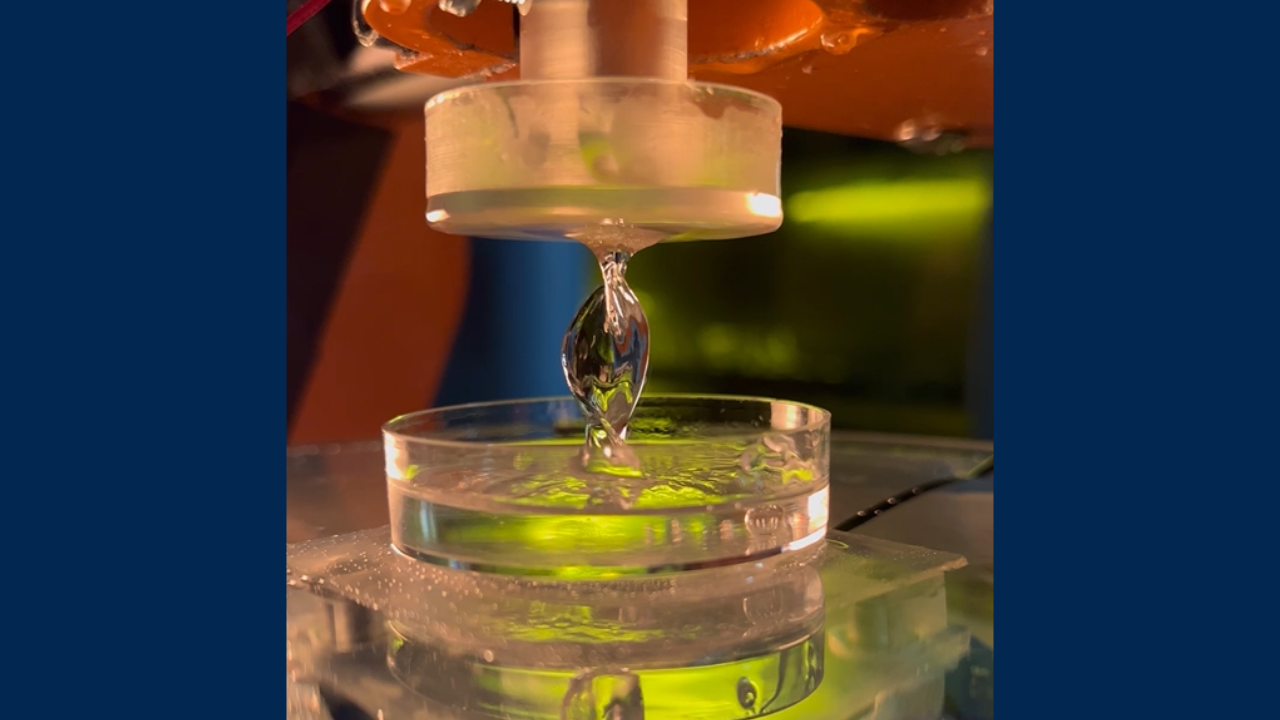
With New Research, 3D Printing with Soundwaves is ‘Science over Fiction’
In an operating room, doctors and technicians work on repairing a broken bone. There are no scalpels, no incisions — the skin is not broken.
No, this is not science fiction, but a potential application of a groundbreaking 3D printing method developed by Mohsen Habibi, an assistant professor of mechanical and aerospace engineering at the University of California, Davis.
In a paper in Nature Communications, Habibi details holographic direct sound printing, or HDSP, which uses high-acoustic pressure soundwaves to project a holographic image and remotely print a two-dimensional version of the image in a polymer material like resin. The material is agitated by the soundwaves, which results in a solid structure.
This 3D printing method is a new breakthrough in printing beyond a physical barrier.
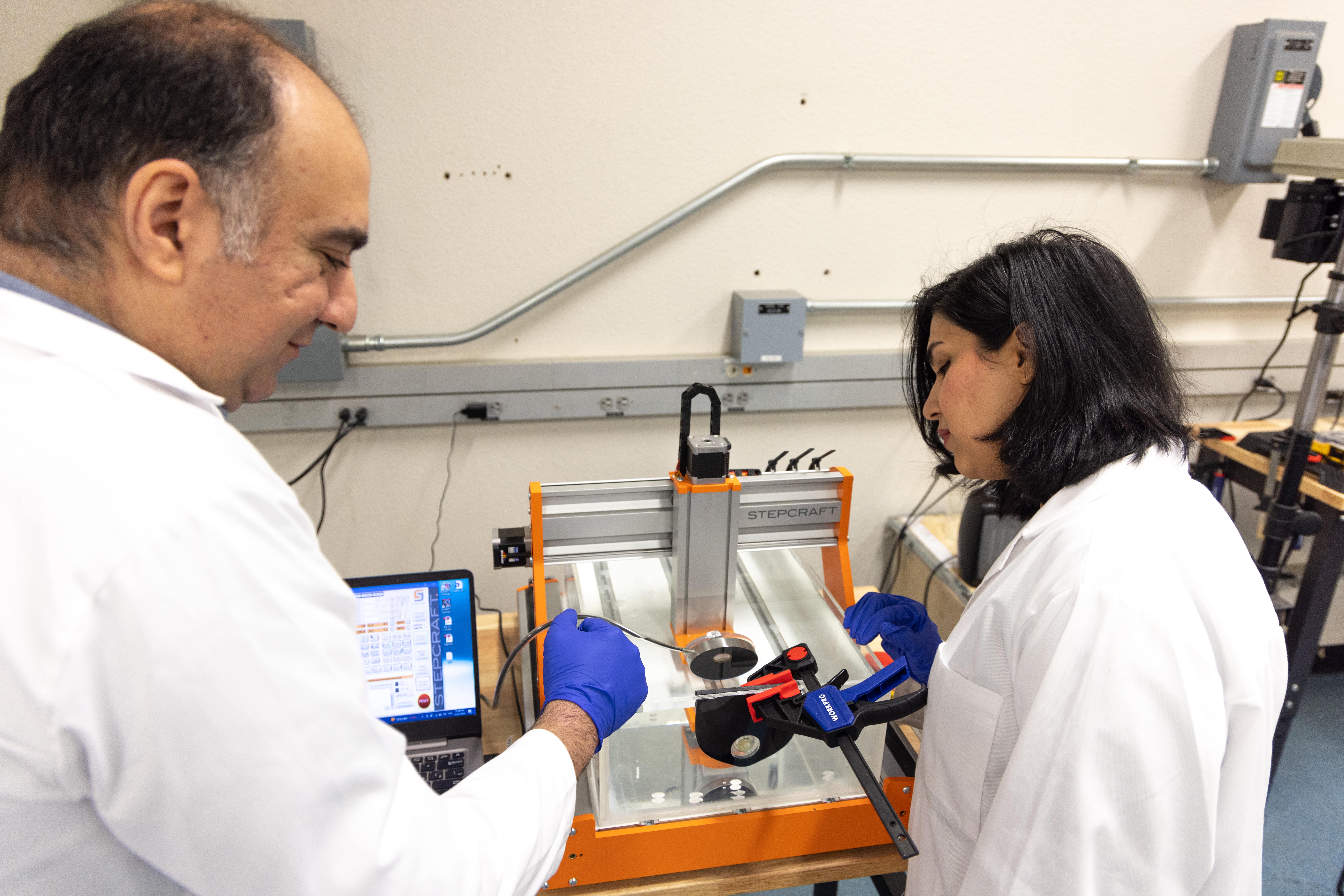
Shaping Sound into Solid Forms
HDSP uses an acoustic holographic picture to project and print the whole image at once.
A holographic picture, explains Habibi, is simply a 3D volumetric picture of an object (think: Princess Leia appearing to deliver a request for help in Star Wars: A New Hope). While holographic images are typically created with light, Habibi uses an acoustic source to create high-pressure zones within a defined environment.
“With HDSP, I have a hologram that projects a holographic picture of a circle at a certain location,” he says. “That location is inside the build chamber that I filled with material, and it solidifies the picture I want to solidify.”
In these experiments, a robotic arm holds the printing platform. The printing platform hovers above the transducer, which is submerged in water. The build chamber sits between the transducer and the printing platform and is filled with polymer printing material.
The transducer emits high-acoustic pressure sound waves, inducing a sonochemical reaction called cavitation, or very tiny bubbles, in the build chamber and creating solid material. The robot arm moves the printing platform along a complex path to create a shape while simultaneously pulling the printed object vertically out of the build chamber, resulting in a 3D structure.
Soundwaves of the Future
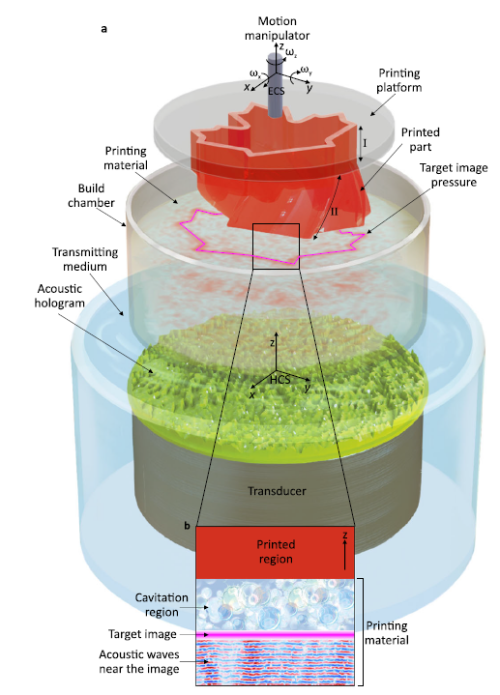
The work builds on Habibi’s previous research in printing with soundwaves for direct sound printing, or DSP. DSP occurs by applying focused ultrasound waves to a polymer that creates cavitation, which then results in a 3D-printed structure.
Habibi says that HDSP is a significant step forward from DSP — a breakthrough in its own right — on the road to 3D printing inside the human body. HDSP prints a two-dimensional picture continuously (without layering) all at once and results in a 3D object, making it much more time-efficient than DSP, which can only print one point at a time and in layers like typical 3D printing.
Thus far, Habibi has been able to create simple geometric shapes using HDSP, including a maple leaf outline, a helix and a “U” shape. When considering the endgame is printing tissues inside the human body, the technique already shows promise.
“Bone, cartilage and similar biological tissues are not really complex in terms of geometry, so they could be projected with only one image,” Habibi says.
While there is still much research to be done before doctors use 3D printing to knit together torn tissues, a la the sick bay of the U.S.S. Enterprise in Star Trek, breakthroughs like HDSP bring us closer to that reality. Habibi agrees that though it may sound made up, his research is very real and making progress.
“When people read the 2022 paper in Nature Communications, they mentioned that direct sound printing was science fiction,” he says with a smile. “This is science over fiction.”